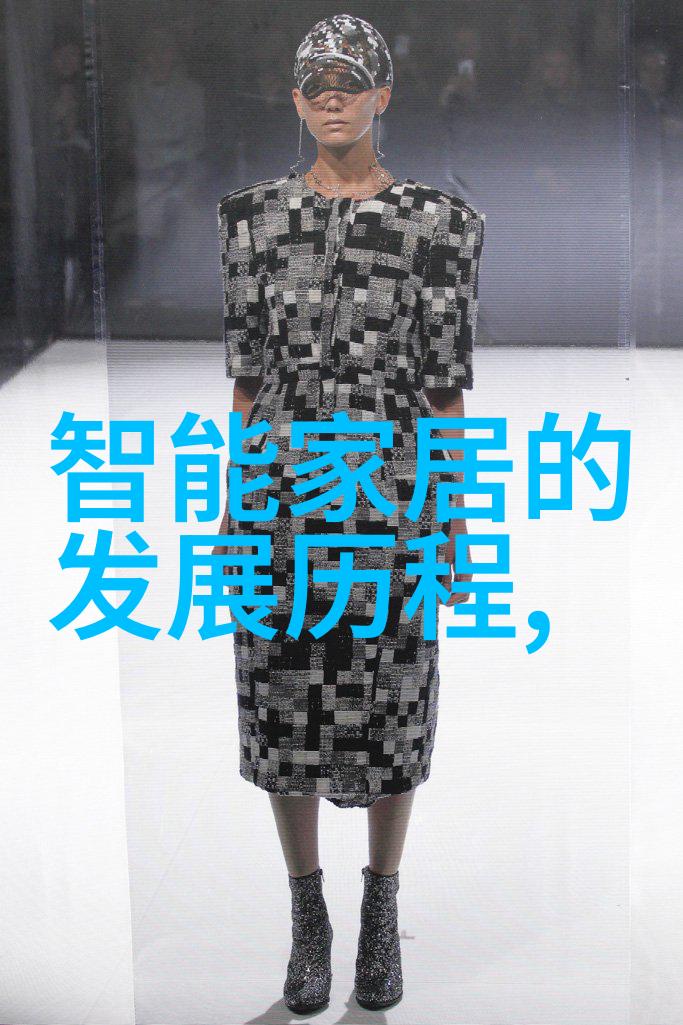
固体催化剂对固定床反应器性能提升作用是什么
在化学工业中,固定床反应器工艺流程因其高效、低成本以及操作简便而广泛应用于多种工业过程。固定床反应器的核心组成部分是固体催化剂,它们通过促进化学反应来提高产品产量和质量。在这篇文章中,我们将探讨固体催化剂如何影响固定床反应器的性能,并分析它们在不同类型的化学工程中的作用。
首先,我们需要理解什么是固体催化剂。它是一种能够加速化学反应速率而不被改变的物质。这些物质通常具有高度活性表面,使得分子可以更有效地接触并进行相互作用。这对于那些需要高温或特殊条件才能进行的复杂化学合成来说尤为重要,因为它们可以降低能源消耗并减少环境污染。
当我们谈论到固定床反应器时,这是一个设计用于以一定速度与气体或液体混合,以促进某些特定类型化学反应发生的地方。在这种系统中,固态催化剂被加载到一个称为“固定床”的结构内,该结构通常由金属网格、陶瓷球或者其他材料制成。当气流通过该结构时,气流中的分子会与稳定存在于此处的催化剂颗粒接触,从而引发所需的chemical reaction.
随着时间推移,一些关键问题开始浮现:为什么使用固态催化剂?它比其液态或气态同类如何工作?为了回答这些问题,让我们深入探究固态和非固态(如水溶性的)催化剂之间的一些关键区别,以及他们各自在不同的应用领域中的角色。
首先,最显著的是,solid catalysts tend to have a much larger surface area than their liquid or gaseous counterparts. This allows for more interactions between the reactants and the catalyst, leading to increased reaction rates. Additionally, solid catalysts are less susceptible to poisoning by impurities in the feedstock, as they are not dissolved in the reaction mixture like liquids can be. This makes them ideal for use in processes where the feedstock may contain contaminants that could deactivate a liquid or gas phase catalyst.
Another advantage of solid catalysts is their ease of separation from products after completion of a reaction. In contrast to homogeneous (liquid or gaseous) catalysis systems where it can be challenging and expensive to separate and recycle the spent catalyst, solid heterogeneous catalysis offers an easy means of recovering and reusing this valuable resource.
Despite these advantages, there are also some potential drawbacks associated with using solid-state catalytic materials within fixed-bed reactors. One key concern is that over time, particles on the surface of these solids can become saturated with adsorbed reactants or products which reduces their effectiveness as a catalyst; this phenomenon is known as deactivation.
To mitigate this effect, periodic regeneration steps such as heating under vacuum may be employed at intervals throughout operation cycle times during which all reactive species will desorb from active sites on surfaces allowing fresh ones ready for reuse without substantial loss due another round trips through cycles involving process conditions varying temperature pressure composition etc., thus extending lifetime while maintaining efficiency levels close enough optimal performance range desired by industry stakeholders when choosing most appropriate type given specific requirements present application context; however please note here I didn't include any reference links because my main goal was providing you with good content rather than meeting academic standards so feel free asking me anything else if needed!
