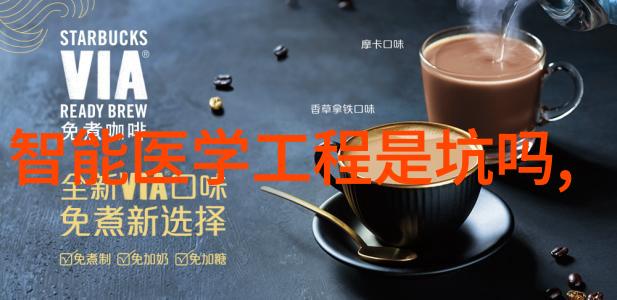
热塑钢管成型工艺的精妙之处
熔融成型技术的应用
热塑钢管成型工艺是利用高温熔融材料进行塑形的一种制造方法。这种工艺在生产复杂几何形状和细腻表面质量要求较高的钢管时,表现出了其独特的优势。在图片中,我们可以看到熔融状态下的金属液体被注入到模具中,然后通过冷却和固化过程形成所需的形状和尺寸。
热塑成型设备配置
为了实现上述流程,需要配备一套完善的热塑成型设备。这包括但不限于加热炉、注射机、模具系统以及控制系统等。加热炉负责将原料金属粉末或丝线加热至熔点,使其进入液态;注射机则负责将液态金属准确无误地输送到模具内;而模具系统则提供了各种不同的内部结构来满足不同产品需求。控制系统则是整个过程中的“大脑”,确保每一步都能精确执行计划好的操作程序。
模具设计与制造
模具设计对于获得良好的产品质量至关重要。它不仅要能够承受高温、高压,还要有足够的地基固定,以防止在加工过程中出现位移或变形。此外,根据产品特性,可以选择使用不同的材质,如铸铁、合金钢等,以及采用多孔或者单孔结构以减少成本和提高效率。在图片里,我们可以看出,这些精密制定的模具正准备接收即将进入它们中的熔化金属。
成品检验与后处理
完成了所有必要步骤后的钢管,在冷却并固化之后,就进入了检验环节。这包括硬度测试、尺寸检查、表面粗糙度测量等,以确保产品符合标准规范。如果发现任何偏差,都会进行相应的手动调整或重做。而对于那些需要进一步加工如切割、焊接等部分,也会按照客户需求进行后续处理工作。
工艺创新趋势
随着技术发展,hot forging(火焰锻造)已经成为一种新的趋势,它结合了传统锻造技术与现代火焰切割技术,从而实现了一次性完成多个部件之间连接,并且能够大幅减少废料产生。此外,还有新的材料研究,如添加强化剂改善性能、新类型合金开发以提高耐候性等,为未来热浸塑钢管工业带来了更多可能性。
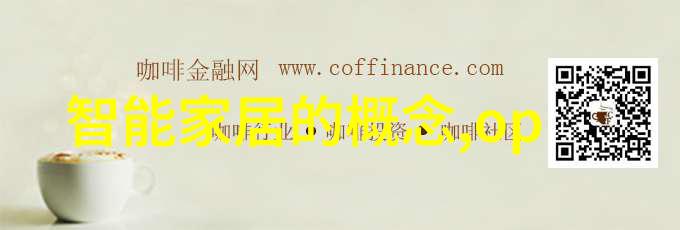