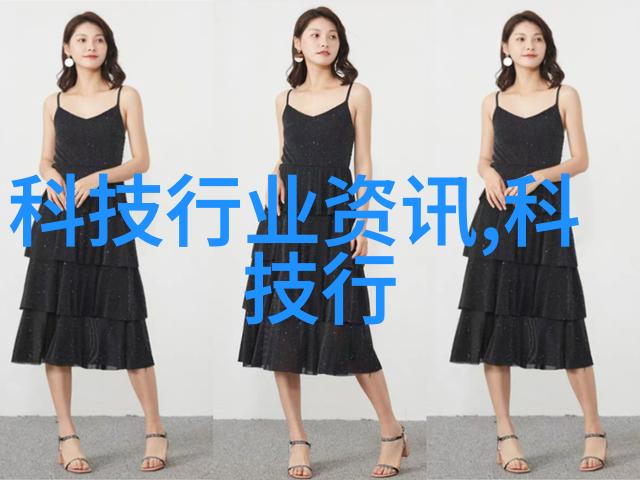
提高效率与降低成本通过精益生产原则改进反应釜设计图
在化学工程和制药行业中,反应釜是进行各种化学反应的关键设备。其设计不仅关系到产品质量,还直接影响到了生产效率和成本控制。在追求高效、节约资源的今天,精益生产原则被越来越多地应用于反应釜的设计中,以实现既提高产量,又减少浪费的目标。
精益生产原则介绍
精益生产是一种旨在最大化价值流动,同时最小化浪费的管理哲学。这一理念源自汽车制造业中的丰田公司,并由詹姆斯·温特(James P. Womack)等人广泛推广至其他行业。精益方法强调持续改进,不断寻找并消除所有类型的浪费,包括时间、材料、资金和人员等方面。
反应釜设计图优化策略
为了有效实施精益思维,在绘制反应釜设计图时,我们可以采取以下几个策略:
1. 减少过剩容量
在传统工艺中,往往会为潜在扩张或未来需求预留一定容量,这样做虽然有助于灵活性,但同时也意味着更多未使用空间造成能源消耗。此时,可以采用模块化设计,让单个反映可水平扩展以适应需求增长,而不是一次性投入大量资源构建一个巨大的反映。
2. 简化操作步骤
复杂操作步骤不仅增加了员工培训时间,也可能导致人为错误,从而影响整体产出速度。简化操作流程,如减少装卸次数,或采用自动化设备,可显著提升工作效率并降低劳动力成本。
3. 实施循环利用
废弃物如废气、废水或固体废物如果能得到回收利用,就可以极大地减少对环境和经济资源的负担。例如,将污染较高或难以处理的大气排放转变为有用的热能或者电力输入,则可以进一步节省能源开支。
4. 提升内存储能力
提高内存储容量对于避免频繁清洁及更换器材具有重要意义。一旦确立了一个良好的内部清洁系统,可以最大限度地延长每次使用之间必要间隔,从而降低维护成本和增加机器使用寿命。
实例分析:如何应用精益思维优化反映设计图
假设我们正在开发一种新的药品,其研发周期紧迫且需要大量实验室试验。通过应用精益思想,我们可以将整个过程分解成若干小步骤,每一步都要经过严格评估,以确保每项任务尽可能高效完成。在这个过程中,一些关键点包括:
缩短试验周期:通过合理安排实验顺序以及选择能够快速提供初步结果的一些测试方法。
智能装置安装:安装自动数据记录系统,使得实时监控成为可能,便于即时调整实验条件。
标准件库建设:建立标准件库以便快速获取所需零部件,从而缩短设备准备时间。
交叉验证程序:引入交叉验证程序来检查结果准确性并发现问题前提下避免重复实验。
结论
通过将精益思维融入到反映设计图之中,我们不仅能够显著提升工作效率,而且还能够降低总体成本,包括但不限于能源消耗、材料损失以及员工培训费用。这对于当前竞争激烈且压力山大的人口健康领域尤为重要,因为它有助于企业保持市场竞争力,同时创造出更加可持续发展下的产品。而这正是现代工业革命所要求我们不断探索的问题解决方案之一。