
固定床反应器工作原理剖析
定义与分类
固定床反应器是一种常见的化学工程设备,它在工业生产中广泛应用于催化剂固体表面上的化学反应。根据操作条件和设计特点,固定床反应器可以分为多种类型,如气相流动层、液相流动层、以及混合流动层等。这些不同类型的固定床反应器各有其适用范围和优势。
工作原理概述
fixed-bed reactor, also known as a trickle bed reactor or a packed bed reactor, is a type of chemical processing equipment that uses the solid surface of catalysts to facilitate chemical reactions between reactants in gas and liquid phases. The key principle of fixed-bed reactors lies in maintaining the stability and uniformity of reaction conditions by ensuring consistent flow rates and temperature control throughout the catalytic process.
催化剂固定的重要性
The concept of 'fixed' in fixed-bed reactors refers to the fact that the catalyst particles are immobilized within a bed or layer inside the reactor vessel. This immobility allows for efficient heat transfer between hot gases flowing over or through the catalyst particles, which helps maintain optimal reaction temperatures while minimizing energy consumption.
流体分布及控制
To ensure optimal performance from fixed-bed reactors, it is crucial to properly distribute fluids (gas and/or liquid) throughout all layers of active catalyst within the reactor vessel during operation. Factors such as inlet fluid velocity, pipe diameter size, and distributor design play significant roles in achieving uniform distribution patterns for both mass transfer efficiency and overall productivity.
冷却系统与温度管理
Temperature management plays an essential role in controlling reaction kinetics for successful outcomes with fixed-bed reactors. By incorporating effective cooling systems into these designs—such as shell-and-tube exchangers or internal spiral coolers—the risk associated with overheating due to exothermic reactions can be minimized while allowing precise control over desired operating temperatures.
维护与替换策略
Over time, deactivation occurs due to various factors like sintering (particle growth), poisoning by impurities present in feedstocks, fouling caused by deposition on surfaces etc., which may negatively impact performance efficiency at some point along with increased pressure drop across beds following particle agglomeration processes leading towards decreased effectiveness; therefore periodic maintenance schedules must be devised including cleaning procedures where necessary followed by replacement when deemed appropriate taking into account specific operational requirements coupled with economic considerations aimed at optimizing production costs without compromising product quality standards
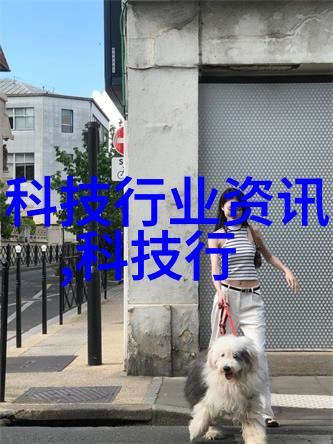