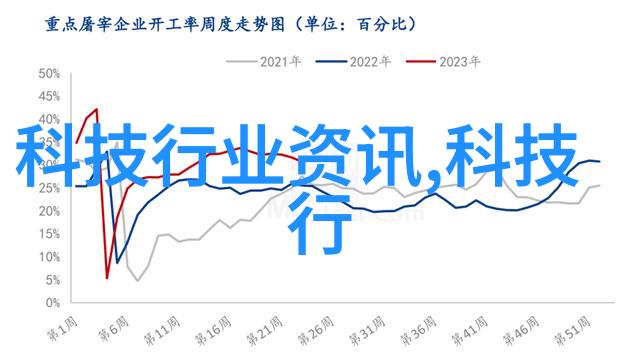
铝单板焊接工艺优化方法研究
一、引言
在现代制造业中,铝单板因其轻质、高强度和良好的耐腐蚀性,被广泛应用于各种领域。然而,铝单板的加工与焊接是实现其最终产品性能的一大关键步骤。由于铝材料本身的特性,如高热膨胀系数、低熔点等,导致其焊接过程相对复杂。这篇文章旨在探讨如何通过优化焊接工艺来提高铝单板的质量和使用寿命。
二、铝单板的特性分析
首先,我们需要了解铝材料自身的特性,这对于选择合适的焊接工艺至关重要。主要包括:
高热膨胀系数:意味着在高温下,金属会膨胀较多,使得焊缝可能产生大的应力。
低熔点:易于熔融,对于避免形成缺陷尤为敏感。
易氧化:表面容易形成薄膜,这可能影响焊料粘附和固化过程。
三、常见的问题及挑战
在实际操作中,由于上述原因,不同类型和厚度的铝单板都会面临一些共同问题:
焊缝裂纹现象:由于温度变化造成的扩张差异导致。
焦渣沉积:空气中的氧气与高温反应生成焦渣,与光滑表面不易结合。
焊丝烧毁或断裂:由于过高温度使得焊丝迅速损坏。
四、优化方法探讨
为了克服这些问题,可以采取以下措施进行改进:
改善炉区环境:
使用无油氮保护气体以减少氧气进入炉内。
调整炉温,以避免过快或过慢的加热过程,从而降低应力集中。
提升预处理技术:
清洁表面的锈迹和油脂,以确保良好的金属连接界面。
使用化学处理去除表面的外层氧化层,让金属更好地与涂层结合。
选择合适型号:
根据不同的工作条件选用不同类型(如TIG/AG/TIG+AG)以及电极尺寸大小,以及填充剂等参数配置。
改进设备设计:
设计更加稳定可靠的地台架,以防止振动影响到精密控制系统。
培训操作人员:
对操作人员进行专业培训,让他们能够熟练掌握各种技能,并理解每种情况下的最佳做法。
五、案例分析
为了验证上述理论上的优化建议,我们可以参考实践中的案例。在一次生产线上的改进行动中,一家公司发现了以下几个具体措施带来的效果提升:
采用更先进的人工智能辅助控制系统,使得炉温调节更加精确,同时减少了人为操作错误率降低到了10%以内,从而显著提高了产品质量水平;
对生产流程进行彻底清洁并实施严格管理制度后,其产品缺陷率从原有的20%下降到了5%,这直接反映出预处理阶段对最终成品质量影响巨大;
3 在采用特殊护罩设计后,无论是在室外还是室内环境,都能有效隔绝空气污染物,因此解决了焦渣沉积问题;此外,该设计还让灯光照射均匀,从而有助于观察 Welding 过程中的细节调整;
4 最后,在运用新型导电补偿结构之后,试验结果显示整个 Welding 工序时间缩短约30分钟,而且安全事故发生几率也显著减小,因为手动操作部分被自动控制所替代,因此保障了员工健康安全;此举同时也促使企业进一步投资研发新的自动装配机器人,为未来的生产效率提供更多支持。
六、结论
通过以上提出的多种策略我们可以看到,不同程度的事故事件都可以得到有效治理。而这些经验教训再次证明了不断学习创新是保持竞争力的关键。在未来发展趋势中,将继续深入研究如何利用新技术、新材料以及其他创新手段来进一步提升 铝 单 板 的 质量 与 效益。
