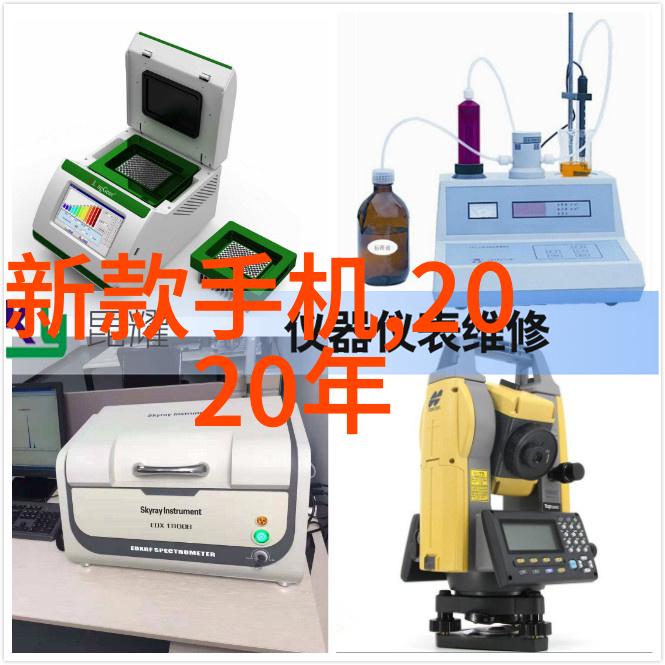
如何预防反应器中出现压差过高的情况
在化学工业的生产过程中,反应器是实现物质变化、合成新产品的关键设备。然而,在操作过程中,如果反应器中的压差过高,这不仅会影响到产品质量,还可能导致设备损坏甚至安全事故。在此,我们将探讨造成反应器压差过高的原因,并提供建议,以避免这一问题。
首先,了解为什么会发生压差过高非常重要。通常情况下,压力升高等问题是由以下几个因素引起的:
温度控制失效:温度与液体或气体的状态密切相关。当温度升高时,物质膨胀,从而增加了系统内的总体容量和相应的工作量。这意味着更大的流量需要通过较小的地面,因此,对于保持稳定的流速来说,可以产生很大的压力增益。
反应速率变化:在某些化学反应中,如果加入剂或者催化剂数量不足以支撑所需转化率,或反响速率太快,则可能导致对流动力学参数(如流量、混合时间)发生显著变化,这也可能引发系统内部排列不均匀,从而造成局部阻塞或渗透现象。
材料积累:在长期运行后,由于材料逐渐积累,如沉淀物或污垢,这种现象有时候称为“植物生长”,可以限制管道内有效通径,使得必要时要通过相同面积上输送更多水分,也就是说增加了水头,同时降低了能量传递效率。
管道弯曲及连接处故障:管道弯曲处由于剧烈变形使得局部弹性模量下降,即使未达到断裂点,也可能导致结构强度减弱。此外,不当连接和焊接技术同样会削弱管道壁厚度,从而降低其承受能力。
设备维护疏忽:如果未经常检查并进行适当维护,比如清洁滤网、更换磨损部分等,那么随着时间推移设备性能将不断恶化,最终导致工作条件恶化至无法满足设计要求,而表现出越来越严重的问题,如突然间超出设计范围之外的事故情况。
为了预防这些问题,我们可以采取一系列措施:
首先,对于涉及热处理阶段的一些化学工艺,要确保能够精确控制温度,以便保证最佳产出的同时避免极端环境给予设备带来的破坏。对于一些特别敏感的大型机组,可考虑安装自动调节装置以监控并调整温室条件从而避免任何突发事件;另外,可以定期对热交换表面进行清洁,以减少交换系数随时间变化所引起的问题。
其次,要建立一个完善且可靠的手段去跟踪和记录所有相关数据和参数,这包括但不限于进口/出口流量、输入输出温度以及最终产出的质量指标。如果检测到任何异常,都应该立即停止操作,并进行彻底调查以确定是否存在潜在风险,以及采取什么样的措施来解决这些问题;同时,将发现的问题作为改进计划的一部分进行整改,以确保类似事件不会再次发生。此外,当遇到特殊场景时,如急停启动,一旦确认安全无虞,就应该尽快重新启动,但前提是已经加固保护措施并做好准备应对紧急情况。
第三,在选择材料方面要考虑耐腐蚀性良好且具有良好的抗冲击性能,因为这直接关系到了整个装置寿命以及它能否持续稳定地提供服务。例如,对于那些容易形成沉淀物或溶解品的地方,可以使用更加耐用的塑料材质,而非传统金属制品,因为后者往往因为氧化作用变得脆弱且易碎落脱落,而且还可能含有微粒级别的人造元素残留,有害健康与环境,所以建议采用全新的塑料制品替代老旧金属件。不过,不论选用哪种材料,都必须经过严格测试以证明其符合标准要求并能承受长期运行下的各种机械荷载和物理力量考验,并根据实际应用需求进一步优化配置方案。
最后,对于那些被认为容易产生大量颗粒的小型配件或者阀门等零件,其每一次润滑都应当遵循严格标准,并实施频繁检查计划以防止泄漏或堵塞的情况发生。而对于那些大规模安装类型,更宜采用自动润滑系统,它们既可以按设定的周期执行任务,又不会因为人为错误丧失准确性。一旦发现任何疑似的迹象,即刻停止运作,并请专业人员介入评估是否需要更新或者修复该配件/组件。
综上所述,在预防reactor pressure drop to high方面我们需要关注多个层面的因素,不仅要注意工程上的细节,比如正确选择材质、合理布置管路架构,还要关注日常管理上的细节,如定期检查维护及规范操作规程。此外,为提高生产效率和保证产品质量,应该投资现代智能监控技术,使得实时数据分析成为可能,让我们能够迅速识别潜在危险并采取行动。在这个不断发展、高科技驱动时代,每一个环节都值得我们的重视与投入。
