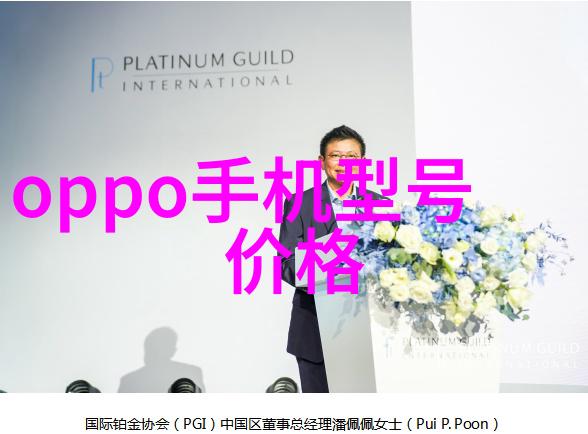
在大规模工业生产中实现动态管式反应器的可靠维护又是怎样的挑战呢
在化工行业中,动态管式反应器因其独特的设计和高效的反应能力而广泛应用于多种化学过程。然而,这些先进的设备也带来了新的维护挑战,因为它们需要精确控制温度、流速和压力等参数来保证最佳性能。
首先,要理解动态管式反应器这种类型设备的一些基本原理。在传统静止型反应器中,物料通常通过静止状态下进行化学变化,而在动态管式反应器中,物料被强制性地搅拌或流动,以提高接触面积并加速化学反 应速度。这使得它具有更快的转化率和更低的能量消耗,但同时也增加了对设备运行稳定性的要求。
对于大规模工业生产来说,这意味着每个部件都必须经过严格测试以确保能够承受长时间、高强度工作负荷。此外,由于这些设备涉及到复杂的机械系统,如泵、阀门、搅拌机等,它们之间相互作用关系密切,因此任何一个部件出现故障,都可能导致整个系统失去功能。
为了应对这些挑战,一家知名化工公司决定实施一个全面的预防性维护计划。这包括定期检查所有关键组件,并使用先进的分析技术(如超声波检测)来发现潜在的问题。他们还采用了基于数据驱动的方法,比如利用实时监控数据来预测哪些部分最有可能出问题,从而提前采取措施进行修理或替换。
此外,该公司还投资了一套模拟软件,以便可以仿真不同操作条件下的行为,并评估不同的维护策略如何影响整体性能。通过这种方式,他们不仅能够优化现有的设施,还能为未来的升级提供指导。
尽管如此,对于这类高度自动化且依赖复杂机械系统的大型装置来说,即使是最精细规划也是不可避免会遇到意外情况。在这样的事件发生时快速响应至关重要,而不是简单地停机修理,每分钟成本损失都会累积起来,因此需要拥有有效的手册与培训程序,让操作人员能够迅速识别问题并采取正确行动。
最后,在考虑到未来发展趋势,我们可以看到随着技术不断进步,无论是在材料科学还是计算机算法方面,都将继续推动我们更好地理解和管理这些复杂系统。这不仅将帮助我们提高效率降低成本,还将增强我们的环境责任感,使得我们能够更加安全、可持续地生产产品,为社会做出贡献。
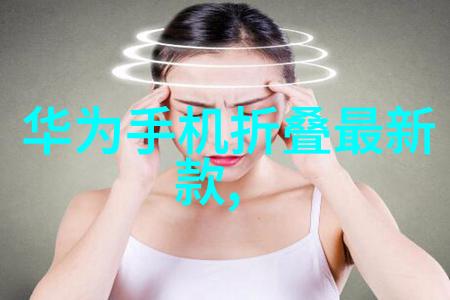