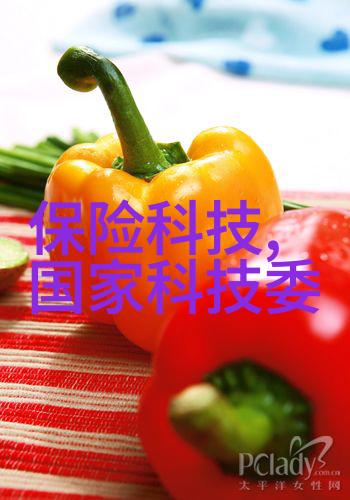
固相合成反应釜与传统溶液法在催化剂使用上有什么区别
随着化学合成技术的不断进步,人们对催化剂的选择和应用有了更高的要求。传统的溶液法虽然在工业生产中占据了重要地位,但它存在一些局限性,如对环境污染较大、操作复杂等问题。在此背景下,固相合成反应釜(Solid-Phase Synthesis Reactor, SPSR)作为一种新型催化剂使用方法,其在催化剂使用上的特点值得我们深入探讨。
首先,我们需要明确什么是固相合成反应釜?简单来说,它是一种特殊设计的设备,可以用于进行无溶媒或少量溶媒条件下的化学反应。这种装置通常由多个小孔或微孔结构组成,这些孔洞可以容纳大量具有活性中心的分子,即所谓的“固定载体”。这些载体能够有效地结合并保持催化剂,使其能在没有额外添加物的情况下稳定工作。这一点与传统溶液法中的自由流动状态有着本质区别。
接下来,让我们来看看固相合成反应釜与传统溶液法在催化剂使用上的主要差异:
催化剂利用效率
固相合成反应 釜 中 的 催 化 剂 通 常 被 固 定 在 特殊 的 支持材料 上,比如 炭 黑、氧核素 或者 金属粒子等,这样做不仅减少了过度脱落的问题,还能够提高每次反应中的催化器效率。此外,由于支持材料提供了一定的空间限制,促使分子更有效地接近活性中心,从而加快了化学转换速度。而在传统溶液法中,自由漂浮的金属离子可能会因为过度沉积或者被其他物质遮盖而导致其活性降低。
环境友好性能
固相合 成 反 应 釜 不 需 要 使用 大 量 无机 溶 励 物 或 有机 solvent,因此显著减少了废水和废气排放,对环境造成较小影响。而且,因为整个过程都发生在支持材料表面,所以涉及到的化学品也远比传统方法要少。对于那些需要严格控制环境因素的人来说,这是一个巨大的优势。
操作简便性
固 相 合 成 反 应 釜 设 计 简 单 直观,不同类型 的 加 工 过程 可以通过改变药品配方 和 加工 条件 来 实现,而且由于操作是在一个封闭系统内进行,所以避免了实验室泄露带来的安全风险。此外,因该设备设计独特,便于自动控制和优化反馈循环,以实现连续生产能力。
规模经济效果
随着技术发展,大规模工业生产已经开始采用固相合成技术。由于这一方法允许单一产品的大规模制造,同时维持良好的质量标准,因此它对于成本效益分析方面显示出巨大的潜力。在大规模生产中,每单位产出的成本节约将会极大地提升企业竞争力。
数据可靠性和重现性的改善
在固定载体上运行时,由于各个位置几乎相同,从理论上讲,每一次实验结果应该都是高度一致且可重复得到。这就意味着科学家们可以更加信赖他们获得的一般规律,并且容易发现异常情况,从而进一步完善研究数据。
总结起来,尽管两种方法都有各自的地位和作用范围,但当考虑到环境保护、操作简便、成本效益以及数据可靠性的角度时,固相合成反应釬展示出了明显优势。如果未来科技继续推进,将会看到更多基于这个原理开发出来的小型、高效、绿色能源解决方案,为人类社会创造新的繁荣时代。
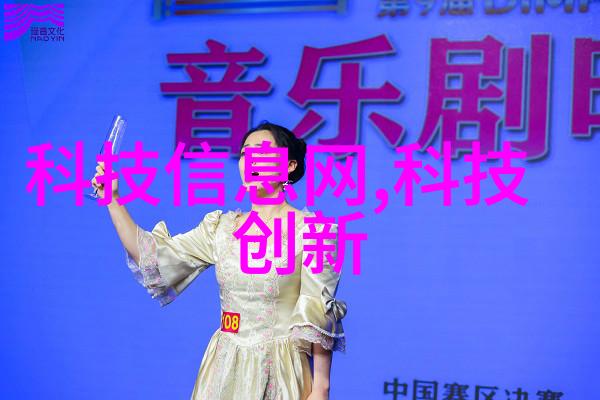